More
than IT 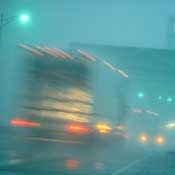
Bridging
the Gap
Between the Factory Floor & Management
Livingston's
corporate priority and imperative is our customers' ability to make
informed decisions with the rich data available through effective process
monitoring. Our expertise targets and ensures critical management
capability of this common thread that runs through the core of industrial
automation. The breadth of our customer base and our depth of experience
with process monitoring tools and data make Livingston's expanding knowledge
base of issues and solutions particularly valuable. Livingston understands
the vital nature of rapid and efficient response to quality issues is
key to our customers' sustained profitability.
Real
time - Every time accountability of the production line's process
data is the crucial element, be it monitoring the making of safety-critical
parts to exacting MVSS or ISO standards, setting and maintaining machine
performance specifications, or maintenance diagnostics and scheduling.
Production line process data is essential for demonstrating compliance
with contract Quality Standards. In today's market, quality assurance
and trace-ability is critical to the enterprise.
Livingston
POD technology bridges the gap between real-time process data from the
production floor and Statistical Process Control (SPC) software systems
and/or Management Information Systems (MIS). Lag-time between process
data and usable SPC statistics leads to batch failure and whole shipments
being rejected. The production floor mantra is "get control of your
process". Livingston's ongoing success is directly dependent upon our
customers' need to use our systems to gain sustained, quantifiable efficiencies
on their production lines. Livingston must be of genuine service. In
technology there are no limits for improvements in performance, function,
or value. Our objective is to be our customers' first choice in bringing
real-time process data "up-the-pipe" to Management where its not data
its usable production information.
Most important,
customers today expect more from their systems and the people competing
for their business. For many customers, process control data is evolving
from a productivity tool to a strategic competitive tool. Fully
networked information systems are being applied across the entire operation
to track critical quality control, materials flow or anticipate production
bottle necks.
When manufacturers
choose a supplier, they expect more than technical proficiency and competitive
cost. Livingston provides reliability, ease of use and support. We
have an integrated spectrum of customer solutions in hardware, software,
training, and creative consulting for unique applications, all tailored
to your organization's specific needs. Expertise from a single source
vendor: Livingston partners with customers to deliver solutions to production
problems, Real time - Every time.
Livingston
& Company’s Resistance Weld Monitoring Systems assess weld quality -
in process - for spot, seam and projection welds. Parameters
such as Current, Voltage, Force, Electrode Displacement, Projection
Weld Setdown and Nugget Growth are processed, analyzed and then compared
to a master "signature." Welds are then accepted or rejected based upon
user-defined tolerances.
Increased
product quality and reduced destructive testing are two of the primary
benefits of Livingston's POD ™ and WeldWise
™ 2400 networked weld monitors. Monitoring weld quality "in process"
can make forty-year-old machines work smart and new machines work
smarter!
|